CM3+
System control by motor is possible without using PLC
AC servo system with built-in control IC and driver

CM3
Challenge to low-cost innovation for small size / mass-produced equipment
AC servo system with integrated controller and driver. Improve the basic performance of stepper motor and make it easier to achieve equivalent performance of servo motor.
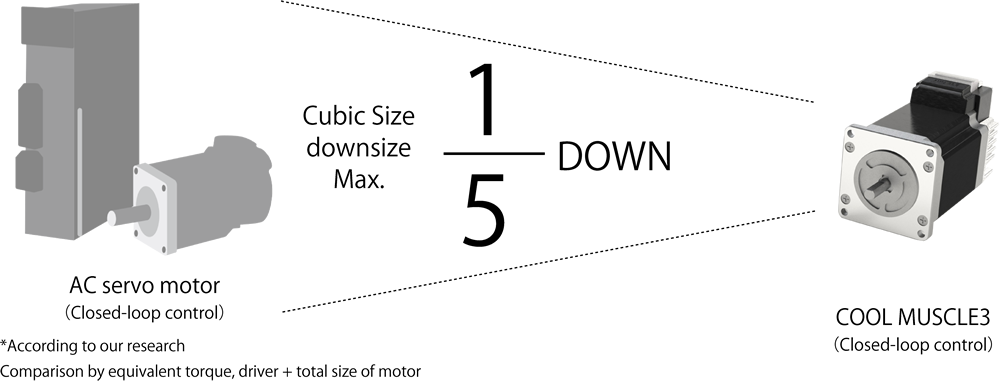
NEWS
- 2025.03.17 Announcement of Exhibition(SSPA 2025) Korea
- 2025.03.06 Announcement of Exhibition(AUTOMATION EXPO 2025) Thailand
- 2025.02.13 65th Birthday Celebrations of His Majesty Emperor of Japan Reception
- 2025.01.20 Announcement of Exhibition (IETF 2025) INDIA
- 2024.08.27 Announcement of Exhibition(SEMICON TAIWAN) TAIWAN
ACHIEVEMENT
Motion Control (OEM application examples)
Robot originally developed by MUSCLE
VOICE
CEO Interview
Japan
(Recruitment motivation for robot manufacturers)
Singapore
(adoption example)
Taiwan
(adoption example)
CONTACT
Please feel free to contact us if there are any problems or questions.
Inquiry