I would like to shorten the tact time of my machine without increasing the total cost, is there a solution?
First of all, in order to shorten the tact time, not only speeding up the motor operation but also responsiveness after applying a start signal is important.
Responsiveness after applying a start signal
Communication speed has become faster and faster, and all devices are often connected via a network. However, controlling all devices at once with a PLC will increase the total cost, and in some cases, may not decrease the tact time of the machine.
By enhancing the responsiveness to an input signal, CM3+ has made it possible to improve the tact time of the machine.
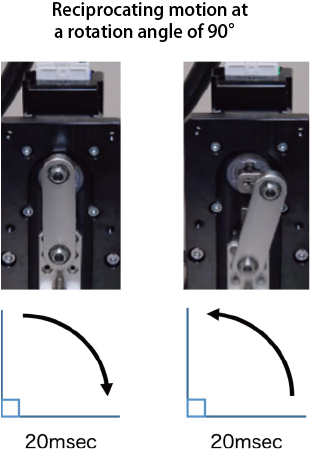
When the sensor signal is controlled by PLC, some time loss occurs depending on the sensor signal input processing time and the standby time of the communication cycle.
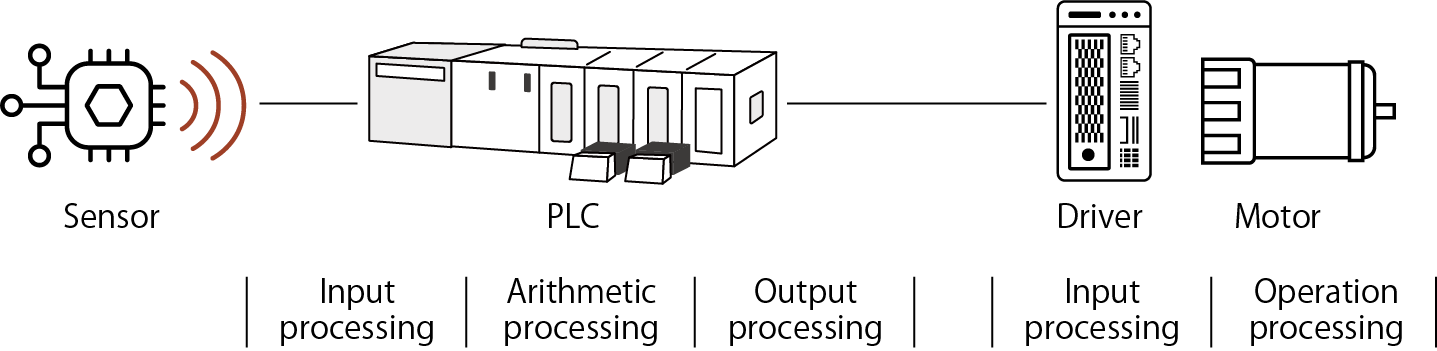
By connecting the sensor signal directly to CM3+, it is possible to start the motor immediately when the sensor is turned on.
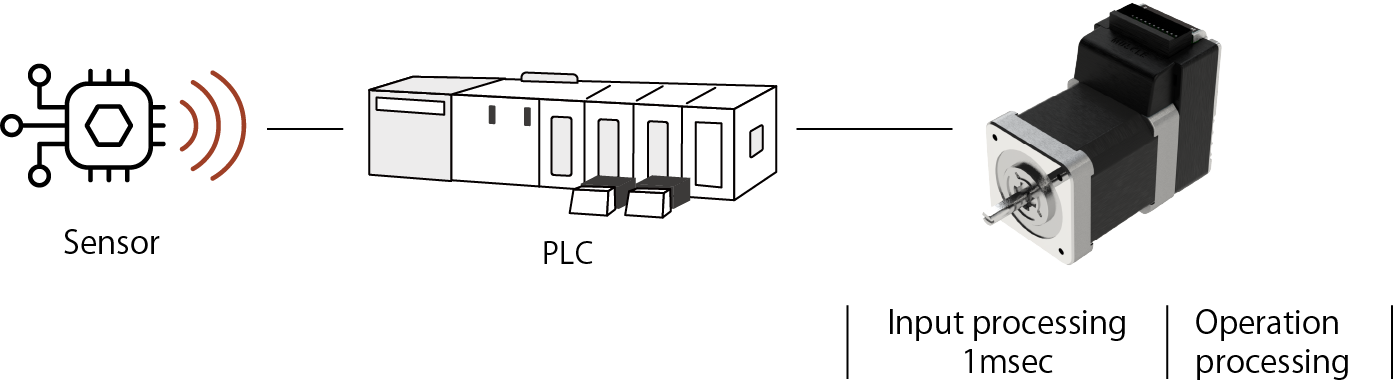
- Isn't the response time 1msec slow compared to the one of MECHATROLINK-III (31.25μs) and EtherCAT (62.5μs), which have a fast transmission cycle?
- If the transmission cycle is set to high speed, the number of motors that can be controlled in the same network is limited due to the limited processing capacity of the PLC.In addition, expensive PLC is required for high-speed processing, which increases the total cost of the equipment.
By minimizing the burden on the PLC and using CM3+ for local high-speed response control, the entire system can be more efficient and cost effective.
Difference between PTP operation and program operation
When PTP motion is commanded from PLC, each positioning completion signal must be processed by PLC.
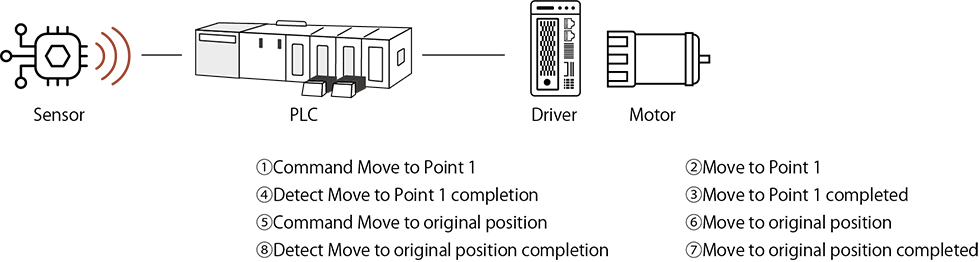
By storing programs in CM3+, CM3+ controls itself as programmed only by applying a start signal.
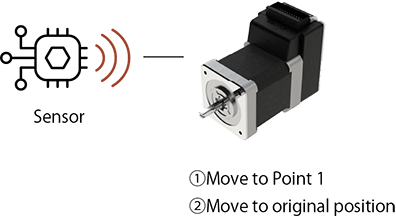
CM3+ program function (Logic Bank)
Integrated microcomputer in the CM3+ lets you perform conditional branching processing and arithmetic processing according to the operating conditions and external environment, and make a wider range of motion control development possible.
* CM3+ has 2 kinds of program, an operation sequence program such as positioning (Motion Bank) and a program that periodically executes conditional branch processing and arithmetic processing (Logic Bank), and those two programs can be executed at the same time.
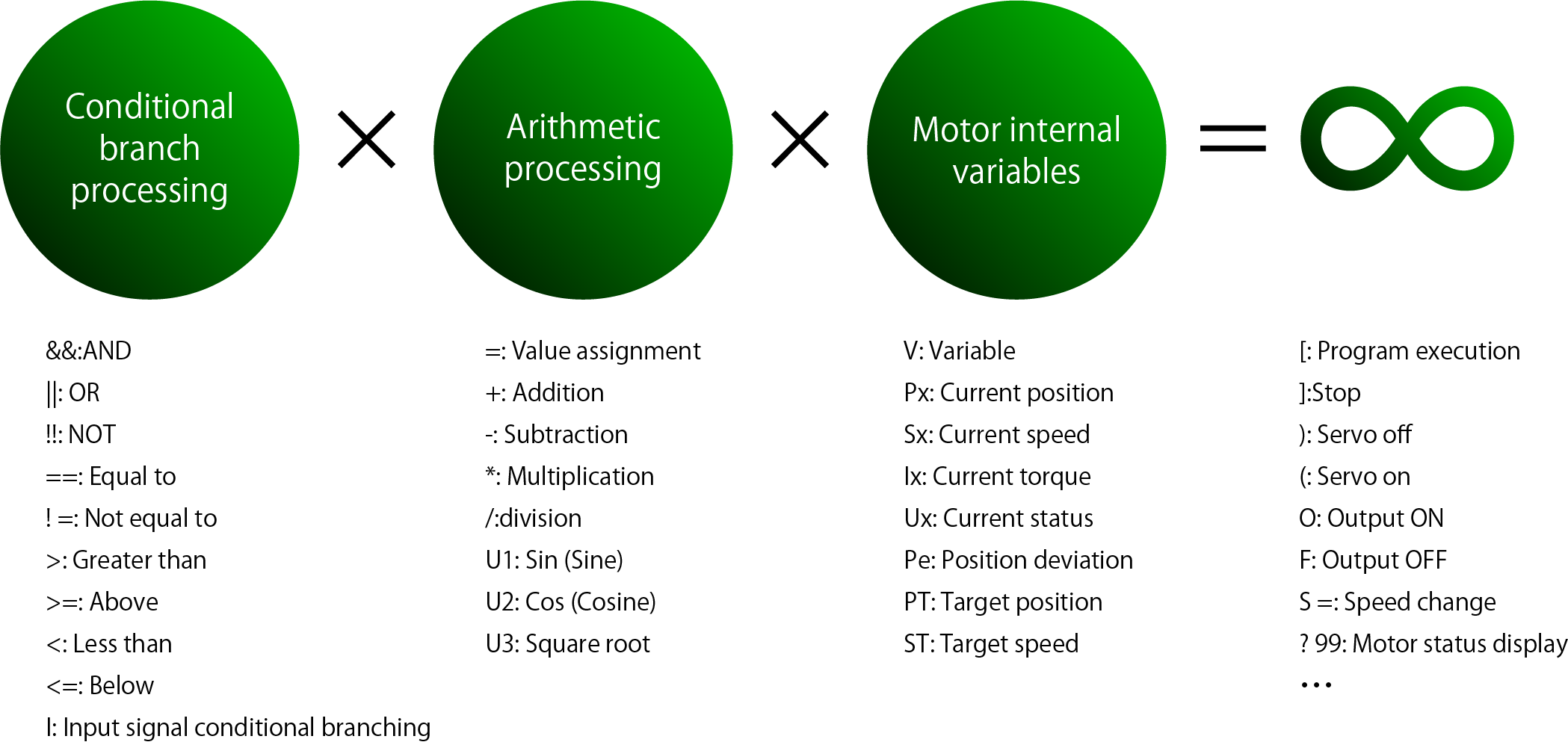
Speeding up motor operation
CM3+ realizes servo performance at low cost by adopting servo control on stepper motor.
Stepper motors are not suitable for applications which requires high acceleration and deceleration due to the risk of step-out, but CM3+ is a servo-controlled motor, so it can produce more torque during acceleration without step-out compared to stepper motors.
- Which is faster, the servo or the CM3+?
- If the application requires high-speed reciprocating motion with a small travel distance, it is possible to use enough acceleration torque in the low-speed range to achieve the same performance as a servo motor.
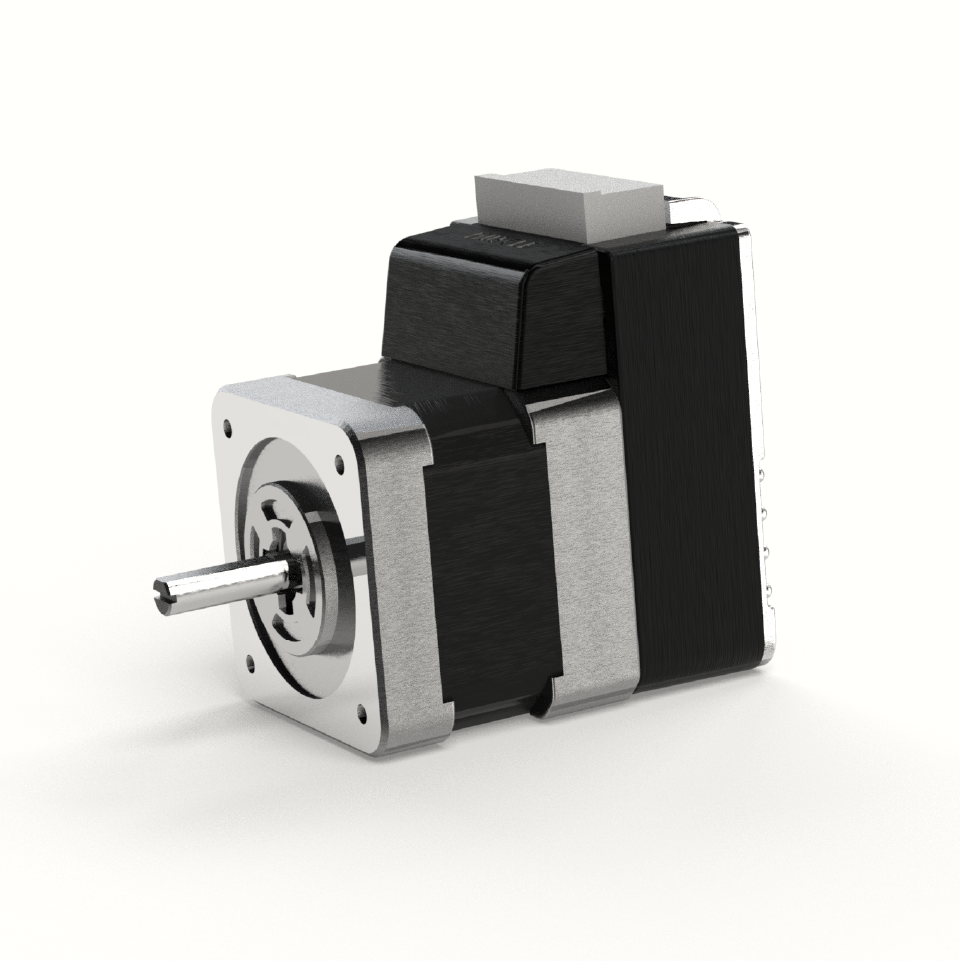
CM3+-17S50A
- Maximum speed:5,000rpm
- Maximum torque:0.32Nm
- Motor size[mm]
- 42
- Motor output[w]
- 60
- Resolution
- Resolution can be selected from 300 to 12,00[pulse/rotation]
- Weight[g]
- 295
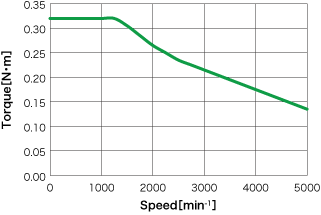
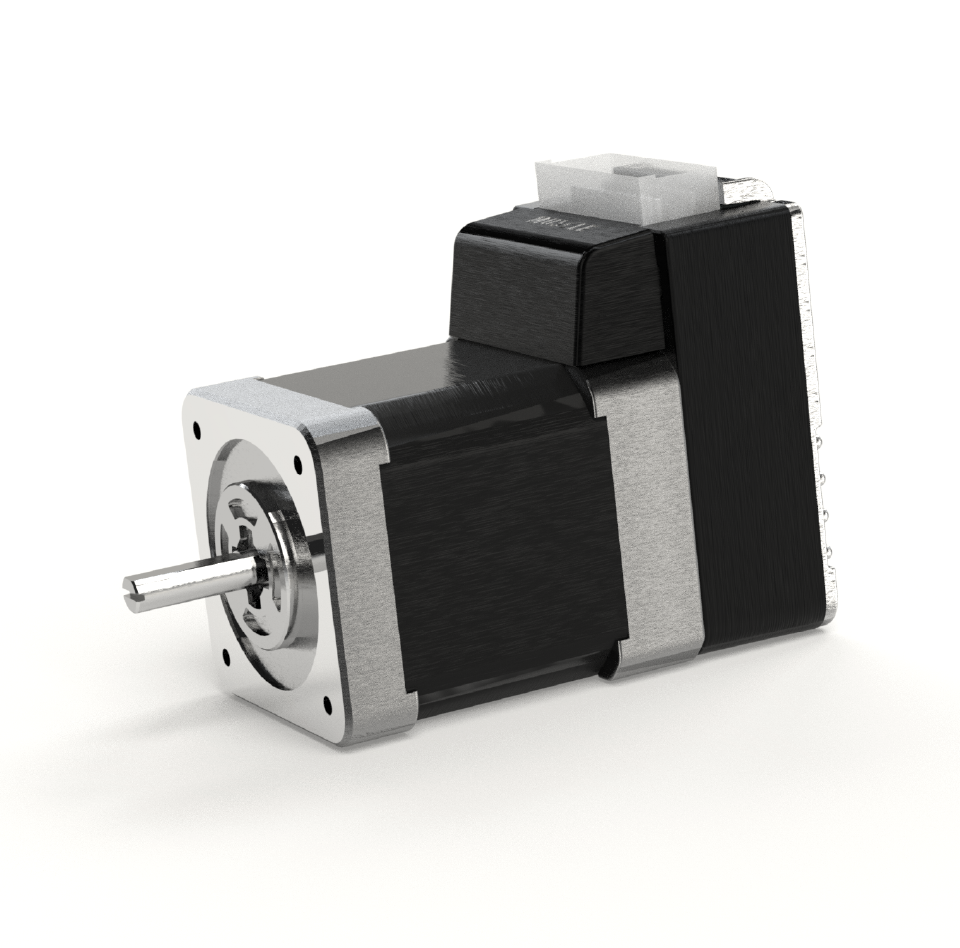
CM3+-17L50A
- Maximum speed:5,000rpm
- Maximum torque:0.65Nm
- Motor size[mm]
- 42
- Motor output[w]
- 60
- Resolution
- Resolution can be selected from 300 to 12,00[pulse/rotation]
- Weight[g]
- 435
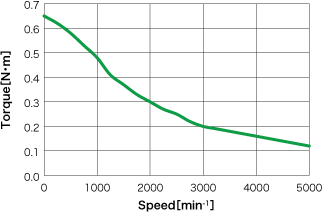
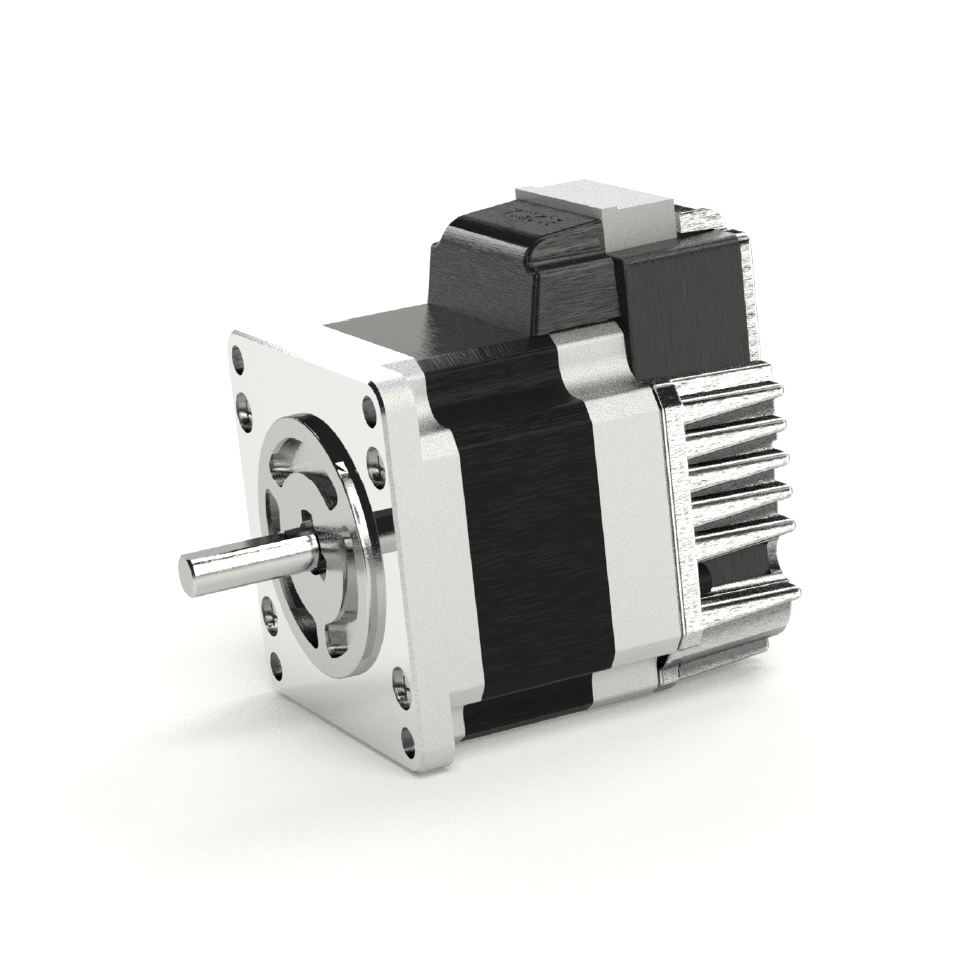
CM3+-23S50A
- Maximum speed:5,000rpm
- Maximum torque:0.45Nm
- Motor size[mm]
- 42
- Motor output[w]
- 80
- Resolution
- Resolution can be selected from 300 to 12,00[pulse/rotation]
- Weight[g]
- 525
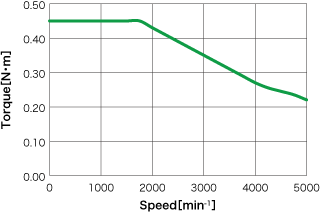
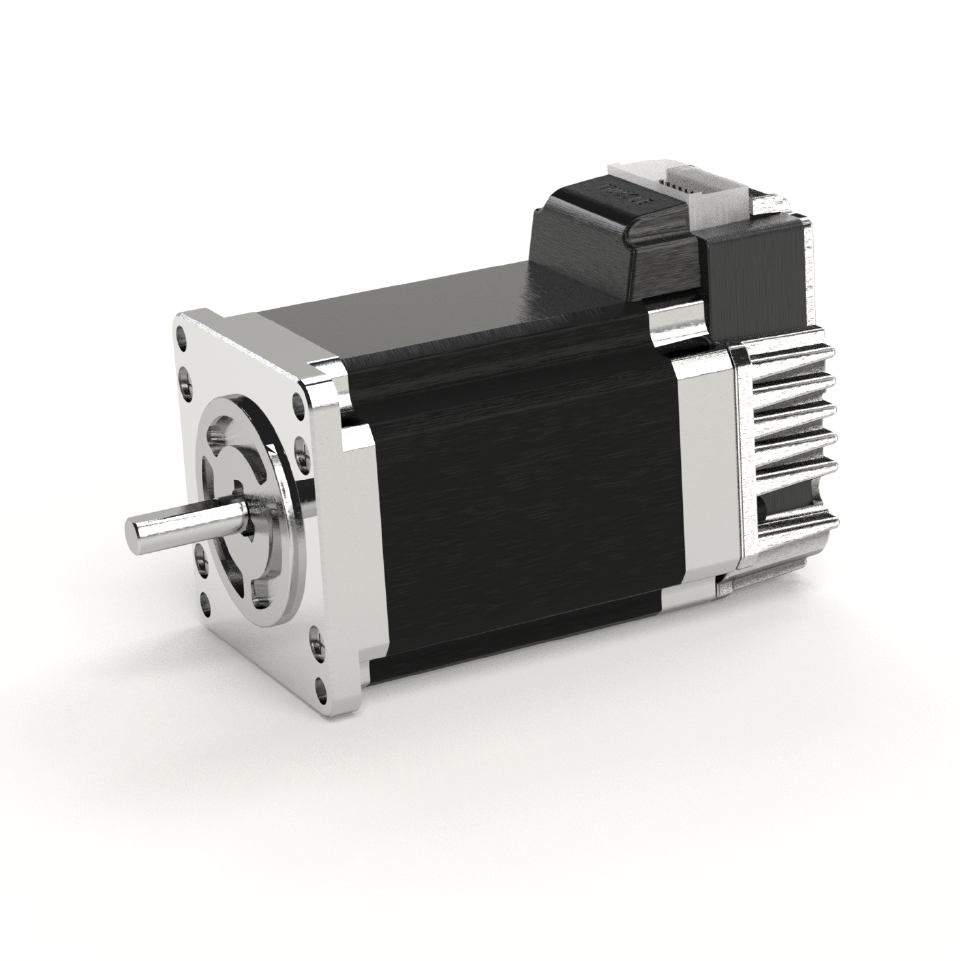
CM3+-23L50A
- Maximum speed:5,000rpm
- Maximum torque:1.50Nm
- Motor size[mm]
- 42
- Motor output[w]
- 100
- Resolution
- Resolution can be selected from 300 to 12,00[pulse/rotation]
- Weight[g]
- 1,050
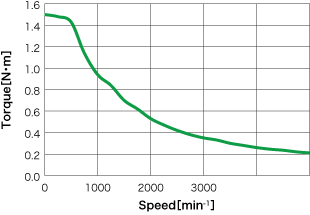